How to Make a Concrete Mix Like Instagram Influencer Alex Zamora – Achieve the Perfect Finish
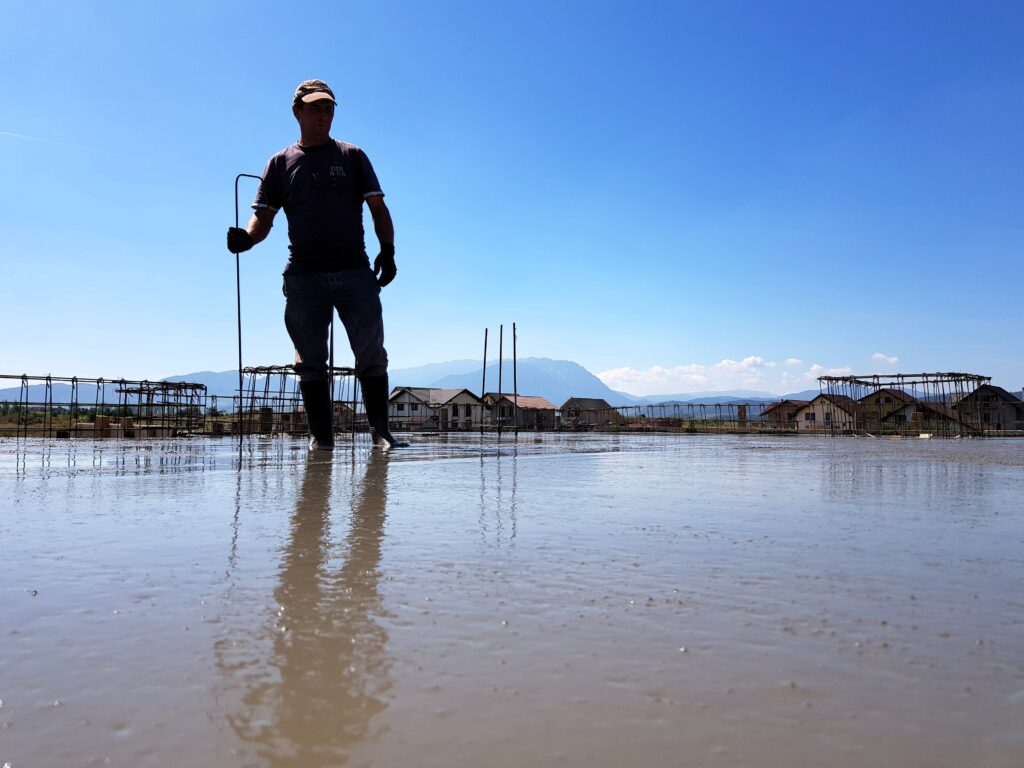
If you’ve been following Alex Zamora on Instagram, you might have seen him mention a 3000 psi concrete mix in one of his posts. This medium-strength design is ideal for planters, countertops, benches, or decorative architectural elements where a high-quality, polished finish is essential. In this article, we’ll break down the recommended mix design, workability tips, and surface finishing techniques to help you replicate that signature Zamora look. Recommended Concrete Mix Design (3000 psi / 20 MPa, Pea Gravel) Material Proportion (by weight) Per Cubic Meter Cement (Type I/II) 1 part 350 kg Pea Gravel (10mm or smaller, rounded) 2.5 parts 875 kg Washed Sand (medium sharp sand) 2 parts 700 kg Water 0.5 parts (w/c ratio 0.50) 175 kg Plasticizer (optional) as needed per manufacturer Approximate Yield: 1 cubic meter (adjust as needed for smaller batches) Target Slump: 75-100mm (3-4 inches) for ease of placement without excessive water addition. Key Characteristics of this Mix Smooth Finish: The small, rounded pea gravel reduces surface voids and provides a denser, more uniform finish, ideal for polishing. Workability: Moderate workability with good cohesion, reducing the risk of segregation and honeycombing. Shrinkage Control: Lower paste content helps reduce drying shrinkage and cracking. Mix Flexibility: If you want a lighter color, you can replace the pea gravel with 10mm limestone aggregate. Avoid stones larger than 10mm, as they are harder to compact and can leave holes if dislodged. Workability Tips for Different Weather Conditions Cold Weather: Add a rapid-setting admixture to speed up curing and reduce the risk of weak spots. This helps the concrete set properly even in low temperatures. Warm Weather: Use a superplasticizer or workability aid to keep the mix workable longer. This is especially useful if you are working alone and need more time to finish the surface. Surface Moisture: Spray water or a suitable finishing liquid on the surface while troweling to keep it easy to rub and achieve a high sheen. Technique for Power-Float-Like Finish Formwork Setup Use well-sealed, smooth-faced formwork to reduce bug holes and achieve a clean face. Make molds easy to strip – avoid burying screws or nails completely, so they can be quickly removed without damaging the formwork. Initial Placement Pour the mix, ensuring even distribution without excessive vibration to avoid air entrapment. Early Form Removal (Striking) Formwork can typically be removed 2-4 hours after pouring, depending on weather conditions. For example, a slab poured on a hot summer morning can often be walked on by the evening, while the same slab poured on a cold winter day may still be too soft to walk on 24 hours later. Surface Working Use a range of trowels for different edges and textures, including bullnose trowels, corner trowels, and finishing trowels. If you want a rougher finish, use a sponge to rub the surface after troweling. This can help remove small imperfections and create a more textured, natural look. Curing Properly cure the concrete to avoid rapid moisture loss, which can lead to surface cracking. Use a curing compound or keep the surface damp and covered for at least 7 days. Conclusion This mix design and finishing technique will give you a high-quality, smooth concrete surface with a dense, polished finish. With the right preparation and timing, you can achieve professional-level results on your DIY concrete projects, just like those featured by Instagram creators like Alex Zamora.
Sealing Joints Between Plywood Sheets for In-Situ Architectural Concrete Finishes
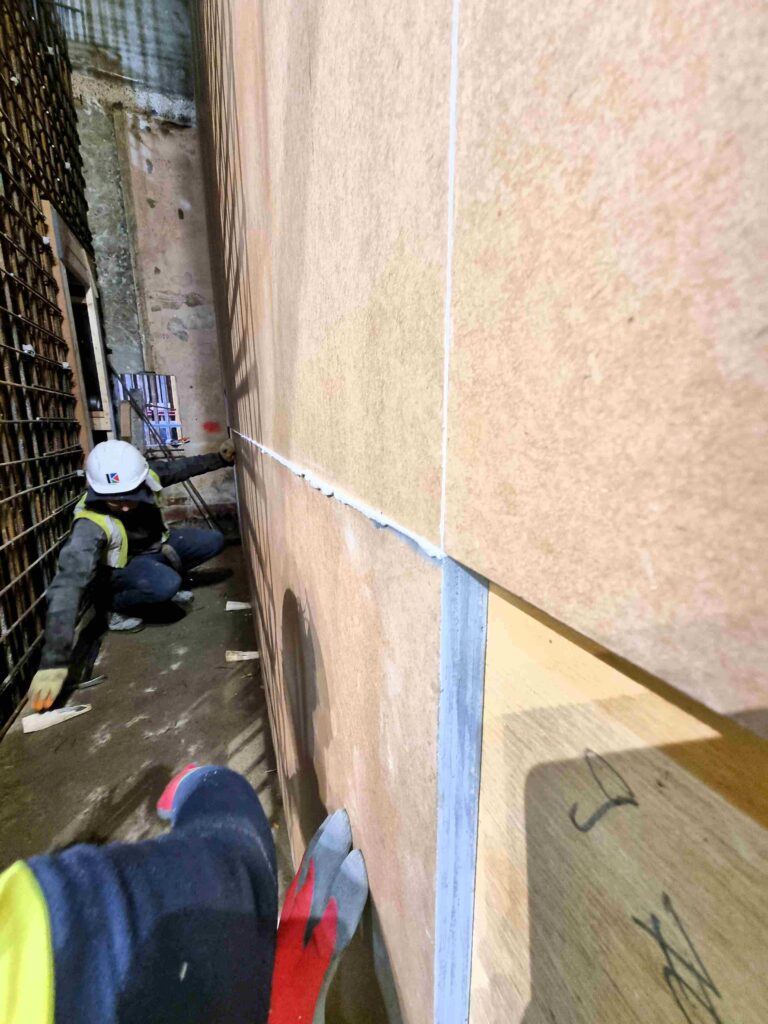
Introduction Producing in-situ architectural concrete with special finishes requires precise treatment of formwork joints. Even when using factory-prepared plywood, poor joint sealing can result in grout loss, surface staining, and visible imperfections. This guide explains how to correctly seal joints between plywood sheets to achieve a flawless architectural finish. Factory Cut Film-Faced Plywood and Formwork Construction We are using factory cut film-faced plywood, specially manufactured with two sides coated in a durable, waterproof film. Full-size plywood sheets will be used wherever possible, and site cutting will be minimized. All shutters are constructed with double layers of staggered plywood sheets, screwed from the back face to avoid visible fixing points. When cutting plywood on site, operatives will use a circular saw with a fine-toothed blade and a straight edge guide. All exposed edges will be treated with a sealing varnish to prevent moisture absorption. Corner joints are cut at 45 degrees and require careful varnishing to prevent localised darkening due to increased water-to-cement ratios. Grout loss at these joints can also lead to honeycombing. Horizontal joints are particularly sensitive because trapped mould release oil can stain the concrete, unlike vertical joints where gravity helps drainage. Why Sealing Plywood Joints Matters – Prevent grout and water loss. – Achieve uniform surface appearance. – Minimise formwork edge damage. – Prevent staining from trapped mould release oil. How to Seal Joints Between Plywood Sheets Sheet Preparation: – Cut edges cleanly using a straight guide. – Apply a high-quality varnish such as Induline SW-910 to all cut edges Butt Jointing: – Butt sheets tightly together with minimal gaps. – Apply a decorator’s caulk like Soudal Decorators Caulk between sheets. This product does not react with wet concrete and physically fills small gaps better than varnish alone. Wipe away excess caulk immediately.Important: Avoid using standard silicone sealants, as they can react chemically with concrete and cause permanent staining. Construction Joints Apply decorator’s caulk to the edge of one plywood sheet before butting the next sheet. Remove any excess material for a clean, uniform joint. Practical Tips – Inspect joints before each concrete pour. – Seal all cut edges and 45-degree corner cuts. – Avoid site cuts where possible to minimise joints. Common Mistakes to Avoid – Not sealing edges properly. – Using reactive silicone that stains the concrete. – Leaving gaps unfilled. – Failing to wipe excess caulk before pouring. Conclusion Sealing plywood joints correctly is essential for achieving premium in-situ architectural concrete finishes. Combining careful cutting, edge sealing with varnish, and gap filling with non-reactive decorator’s caulk ensures defect-free, professional concrete surfaces. This disciplined approach is critical to delivering the high-end finishes demanded by modern construction projects.